はじめに
経営工学に関連したキーワードを学習していて気付いたことがあります。
「多面的な視点が養われ、汎用性がめちゃ高い!」
「技術士二次試験の経営工学部門に限らず、多くの部門に応用可能な知識や方法論が満載!」
ということで、技術士二次試験(経営工学部門)の対策をしている時にまとめてきたキーワード集をほとんどそのままご紹介!
本経営工学キーワードシリーズの記事の特徴として、ある1つのキーワードをについて
- キーワード名
- キーワードを取り巻く背景
- 原理と特徴
- 問題点
- 解決策
- 応用例
- 今後の展望
これらのような、あるいはこれらに近い視点でまとめています。
これはそのまま、技術士二次試験対策に直結するまとめ方です。
このシリーズの記事は次のような方にオススメです!
- 技術士二次試験(経営工学部門)受験予定の方
- 技術士二次試験(経営工学部門以外)の受験予定の方
- 技術士に興味はないけど、経営工学を勉強したい方
ぜひ、それぞれの目的に合わせて勉強にもお役立てください!
キーワード名
発注方式(定期と定量)
言葉の定義
発注方式の説明に入る前に、購買と外注の違い及び、購買管理についてまとめる。
〇購買とは
設備、原材料、部品などを購入する活動。
事務用品やパソコンを購入する活動も「購買」である。
〇購買管理とは
生産活動にあたって、外部から適正な品質の資材を必要なだけ、必要な時期までに調達する手段の体系
〇購買管理の5原則
- 品質管理;最も適した品質のものを購入する
- 数量管理:適正な数量だけ購入する
- 納期管理:必要な時期に購入する
- 価格管理:適正な価格で購入する
- 取引先管理:適正な取引先から購入する
〇外注とは
自社が指定した仕様で外部に部品加工や組み立てを委託すること。
つまり、物の調達ではなく用益の調達と言える。
- 自社で加工・組立を行うより低コスト
- 自社にない技術の活用
- 生産量が変動する際のバッファー
- 生産設備への投資を減らすことによるリスク回避
といったメリットがある。
続いて、定期発注方式と定量発注方式について定義を確認する。
〇定期発注方式
発注間隔を毎日、毎週などと予め決めておき、発注量は使用料に応じて毎回異なる方式。
将来の需要量を予測し、当期末の在庫量をフィードバックして発注量を決定する。
〇定量発注方式
発注する量は毎回同じで、発注間隔が毎回異なる発注方式。
各発注方式の特徴
〇定期発注方式
「発注量の決め方」は以下の式による。
(発注量)=((発注期間+調達期間)の需要の予測値)ー(発注残)ー(手持在庫量)+(安全在庫量)
発注残とは、発注済みであるがまだ手元に届いていない在庫のこと。
調達リードタイムが発注間隔より長い場合に発生する。
安全在庫とは、調達リードタイムの間に、需要変動や不良品の発生など不測の事態が起こっても部品切れが生じないようにする一定数量の在庫のこと。
安全在庫量を多くすると部品切れのリスクは減るが過剰在庫を持つ可能性が高まり、トヨタ生産方式でいう「在庫のムダ」が発生しやすくなる。
逆に少なすぎると、部品切れによるラインストップの可能性が高まる。
安全在庫は以下の式で表される。
(安全在庫)=(安全係数)×(使用量の標準偏差)×√(調達期間)
安全係数とは「許容できる欠品率」で決まる係数。
例えば、許容欠品率が1%であれば、安全係数は2.33になり、許容欠品率が3%であれば、安全係数は1.88になる。
〇定量発注方式
定量発注方式は一般的に定期発注方式より在庫量が多くなる傾向がある。
そのため、定期発注方式より価格の安い部品に適用する。
定量発注方式は、「発注点方式」の一種。
発注点方式とは、在庫量があらかじめ定められた発注点を下回った時に決められた量だけ発注する方式。
家庭生活における、ティッシュや洗剤などの日用品も発注点方式で管理している人が多いのでは。
発注点(発注すべきと判断される在庫量)は、「リードタイム中の推定需要量」と「安全在庫量」の和になる。
- 推定需要量:調達リードタイム中に使用する最低限確保する量
- 安全在庫量:不良品の発生など不測の事態でも欠品を避けるための安全を確保するための在庫量
発注点方式は、発注や管理の手間を省くことを目的としており、安価で使用量が安定しているものに適用する発注方式と言える。
定量発注方式は製造業だけではなく、コンビニエンスストアなどの小売業でもよく使われる発注方式。
在庫保有のメリット・デメリット
在庫とは、将来の使用や需要に備えて意図的に保有する原材料・部品・仕掛品・半製品・製品のこと。
部品の在庫を保有することはメリットとデメリットの両方がある。
〇メリット
- 部品メーカーの納入遅延や不良の発生など不測の事態でもラインストップを回避できる
- 生産計画の急な変更があっても対応しやすい
- 部品の調達リードタイム以下の緊急発注がコストアップになる規定がある場合、コストアップを回避しやすい
〇デメリット
- 保管スペースを多く必要とし、倉庫管理費用がかさむ
- 長期間部品を保管することによって、錆などの品質劣化が生じやすい
- キャッシュフローが減少し、企業の収益が悪化する
- 設計変更が生じた場合に、部品の廃却が発生する可能性が高まる
- 部品の移動や積み替え等の付加価値を生まない作業が増える
在庫保有によるデメリットの解決策
〇経済的発注量
定量発注方式を行う場合、一回の発注量をいくつにすれば費用を少なくできるかは重要なテーマ。
一回の発注量が多いと…
在庫量が多くなり、倉庫の賃借費用等が増える
一方、一回の発注量が少ないと…
情報処理費用や運搬費用が増える
そこで、一定期間の在庫関連費用を最小にする1回あたりの発注量である、「経済的発注量」(EOQ:Economic Oder Quantity)を決める。
(在庫関連費用)=(発注費用)+(在庫保管費用)
とし、その合計を最小化することを考える。
X軸に一回当たりの発注量を、Y軸に費用を表したグラフをイメージする。
発注費用は右肩下がり、在庫保管費用は右肩上がりのグラフとなる。
発注費用と在庫保管費用の合計は極小値を持つグラフとなる。
そのY軸が極小値(最小値)となるときのX軸が経済的発注となる。
数学的に厳密に計算する場合は、1回あたりの発注量をQとして、総費用をQの関数として表す。
この式をQについて微分して、その微分関数=0の時のQの値が経済的発注量となる。
最終結果を数式で表すと、以下のようになる。
(経済的発注量) = √(2Rc/h)
ただし、R:1期当たりの推定所要量
c:1回あたりの発注費用
h:1個1期あたりの保管費用
〇ABC分析
在庫品目には、金額の大小、量の大小、様々なのものがある。
そのため、金額や量に応じて在庫管理の管理レベルを変えることが合理的である。
そのようなコンセプトで行う在庫管理手法としてABC分析がある。
ABC分析とは、在庫品目を金額や量の大きい順に並べて、Aランク、Bランク、Cランクまでの3種類に分類し、管理の重点を決めるために用いる分析手法。
量又は金額を縦軸にとって、部品の品目ごとに降順で棒グラフを作成し、左側からA→B→Cとランク付けすると分かりやすい。
累積線をグラフ上に描き、パレート図として品質管理に用いても良い。
以下、A・B・C各ランクに適した管理手法の例を示す。
手間はかかっても細かい在庫管理を行い、在庫量を少なくすることが合理的な部品に適用する
AランクとCランクの中間的な管理方式とする。
定期発注方式よりは在庫が多くなり、常備品管理方式よりは在庫が少なくなる。
家電業界では一般金属部品等に適用する。
ネジやワッシャーなどが相当する。
安価な部品が多いので、在庫管理の手間を少なくすることに主眼を置く。
補足)常備品管理方式について
常備品管理方式とは、材料や部品などを常に一定量を在庫として保管しておく方式。
常備品に対しては、厳密な在庫管理を必要としない発注方式を採用する。
具体的には、「ダブルビン方式」や「コックシステム」がある。
- ダブルビン方式
- コックシステム
2つのビン(容器)を用意して部品を両方の容器に満たす。
片方の容器から部品を取り出して使用し、もう一方は倉庫などに保管する。
使用している容器が空になったら、もう一方の容器の部品を使い始め、それと同時に1容器分の部品を発注する。
ただし、この方式は調達リードタイムの部品使用量が、1容器分の量以下であることが適用できる条件である。
この方式により、在庫量を正確に管理しなくても部品切れを防ぐことができる。
定量発注方式における発注点と発注量を等しくした方式ともいえる。
水道の蛇口をひねって、必要な量の水だけ使い、使った分だけ水道料金を支払う方式。
かつて、一般家庭への薬の販売方式として普及した「富山の薬売り」と同じ考え方。
この方式は、部品を倉庫に保管し開封するまではメーカーの所有物とみなし、開封したら買い付けをしたとみなす方式である。
応用例
〇発注業務の流れ
①在庫管理
②発注書作成
③確認承認
④発注書送付
⑤受け入れ・検品
⑥支払い
在庫切れを起こさせないために、定期的な在庫確認が必要。
在庫確認の間隔があきすぎると、その間に品切れを起こす確率が高まる。
一方、在庫確認を頻繁に行いすぎると、人手と手間がかかる。
品切れ対策として、一回の発注量を増やしすぎると、過剰在庫となり在庫のムダが発生する。
量と頻度のバランスが重要。
〇発注方法
- 電話:メリットは発注書作成が不要であること。デメリットは、発注の履歴が残らない、伝達ミスのリスクがあること。
- FAX:メリットは履歴が残ること。デメリットは送信ミスのリスクがあること。
- メール:メリットは発注の履歴が残ること。デメリットは受信側がすぐにチェックするとは限らないこと。
- WEB:メリットは発注書作成が不要であること、発注の履歴が閲覧できること。
〇発注業務のポイント
過剰在庫を予防する発注には、2つのポイントがある。
- 発注点管理:あらかじめ決めた発注をかける在庫量に到達しているかチェックする
- 発注方式の選択:定量発注方式/定期発注方式など
発注点の設定がしっかりできていないと、過剰在庫や在庫不足のリスクが高くなる。
また在庫の種類によって最適な発注方式を選ぶことが在庫管理の効率化につながる。
ABC分析などを活用するとよい。
〇発注業務の課題
- 人的ミス:伝票の紛失。転機ミス、情報共有ミス、重複発注、発注忘れ
- 発注内容の不備
- 発注書の不着:FAX
- 完売・欠品の連絡がない
発注には人の手を介した作業が多く、部門間や取引先との連携が必要な点が課題の背景にある。
今後の展望
発注業務の効率化として今後期待されるのが、RPAやIoTを活用した自動発注システムの利用。
- RPA(Robotic Process Automation):FAXやメールの自動送信
- IoT:在庫確認の自動化
自動発注システムを導入することで、次のようなメリットがあります。
- 業務負荷の軽減
- 人的ミスの回避
- 報共有の省力化
- 利益には直結しない業務からやりがいのある仕事へシフト
IoTやRPAを導入することにより、発注の「自動化」や在庫情報や発注状況の「見える化」が可能になり、業務を効率的に進めることができる。
例えば、「スマートマットクラウド」という商品・サービスがある。((株)スマートショッピング)
スマートマットが重さで在庫を検知するというシンプルな仕組みを利用して、残量/残数をスマートマットクラウドに保存。
タグやバーコードの貼り付け・読み取りなどの作業負担もなく、管理画面から実在庫の自動記録、確認ができるため品質管理の現場で重宝。
参考
田島悟:生産管理の基本と仕組み, アニモ出版
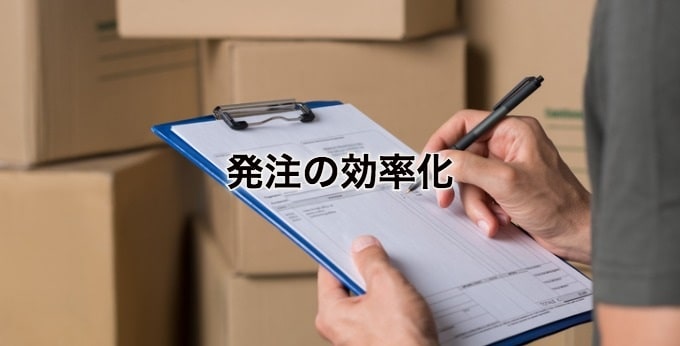
コメント